Removable thermal insulation, removable insulation or thermal jacket are the names most frequently used to refer to the reusable insulation system.
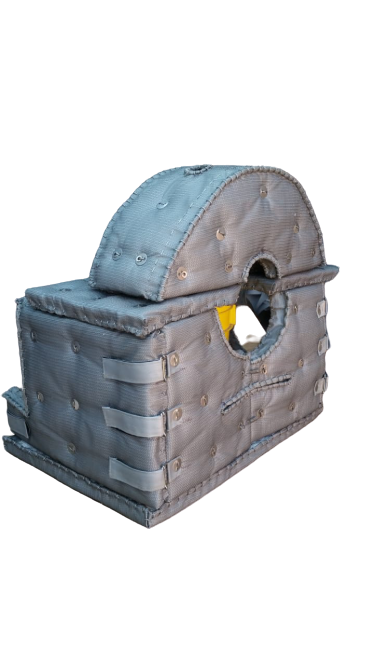
Removable thermal insulation emerged as an alternative to conventional insulation, derived from the difficulties it represents, mainly the fact that it is not removable, that is, once installed it must remain fixed and permanent due to the material with which it is manufactured. (mineral fiber and sheet), which means that when it is removed or uninstalled it is damaged and it is not possible to replace it.
Derived from the above, conventional insulation is not an option to protect equipment that requires frequent maintenance or with complicated geometries in its design, or machinery that requires constant adjustments, therefore, due to so many complications, in the past it was preferable to leave uninsulated equipment.
Nowadays, removable insulation is the solution to these problems, since it has the same advantages of conventional insulation and even more, for example, it prevents heat loss and contributes to achieving an efficiency of up to 95%, it is also a protection for the personnel who operate the equipment, as it acts as a barrier against hot surfaces and, above all, its main advantage is that it is easily installed and removed, without the need for tools or trained personnel. In addition, as it is a reusable insulation, it represents a great competitive advantage.
Removable insulation pays for itself
Based on a study on energy loss carried out at a chemical company in central Mexico, specifically, on valves discovered in the steam supply lines of the boiler area and a pair of heat exchangers, it was discovered that the loss of The energy that the exposed equipment had represented a high economic cost, in the medium and long term, in addition, because the hot equipment was exposed and close to the passage of the employees of said company, there were unsafe areas in the work area.
Additionally, it was observed that the internal maintenance team had few personnel and that the isolation and support activities in facilities required support from contractors and this made their reaction slower in preventive and corrective maintenance, therefore, it was concluded that the option to solve these complications was removable insulation, since no tools or trained personnel are required for installation or removal, in addition to the time required to remove the insulation, check the equipment and put the insulation back in its place, was 2 to 3 minutes, all of which would be impossible with conventional fixed insulation.
Although the initial investment of removable insulation is higher than conventional insulation, in the medium and long term this becomes a saving, because the equipment is inspected and maintenance is provided on average every 12 months, if insulation is placed. Conventionally, the investment in new insulation would have to be made in the same period (every 12 months); in addition, the payment of the technician who installs it must be added.
The above would not happen with removable insulation, this being one of its main advantages, therefore, currently removable thermal insulation is highly demanded and known in the industry, we find it in valves, flanges, tanks, reactors, turbines, pumps, some pipes, heat exchangers, exhausts, filters, etc.
Detachable/removable thermal insulation composition
Removable thermal insulation consists of 3 main components:
1- External protective cover, also known as “cold face”, designed to be a protective shield against the environment; composed of fabric based on fiberglass, silica with silicone or Teflon treatment.
Operating temperature: (-55ºC to 300ºC)
2- Insulating filling, typically made of fiberglass or ceramic fiber that provides heat containment; Thickness varies from 1 to 4 inches, depending on the amount of heat reduction required in the application.
Temperature from (-40ºC to 1200ºC)
3- Internal lining, also known as “hot face”, can be made of stainless steel mesh, fiberglass fabric or treated fabric, which helps as a vapor barrier or fluid protection barrier.
Temperature from (-55ºC to 1260ºC)
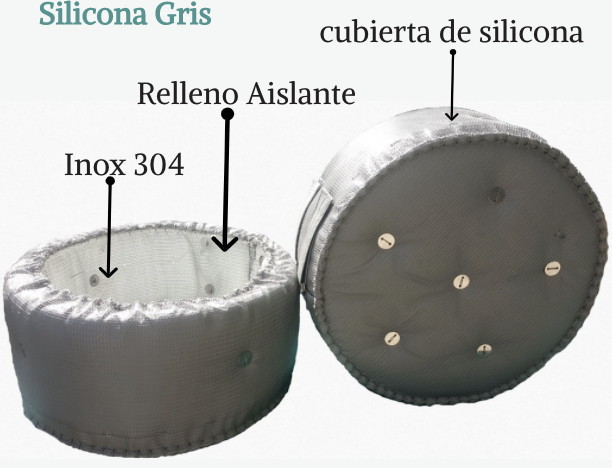
Before manufacturing the insulation, the conditions of the equipment and also the scope and purpose of the insulation must be studied. Therefore, it is suggested to first ask the following questions:
- What equipment is required to isolate?
- What is the constant operating temperature?
- What temperature is requested or allowed on the external face of the equipment?
- What weather conditions will the material be exposed to?
- Will it be in contact with any chemical agent?
- What will be the frequency of insulation reinstallation?
Once you have the answers, the VEMORI thermal insulation supplier will be able to design the insulation that suits your needs; At VEMORI we carry out a thermal study and combine the necessary materials to guarantee the efficiency and durability of the thermal insulation. In addition, we offer different adjustment or tie-in options for the insulation so that the jacket is perfectly installed on the equipment.
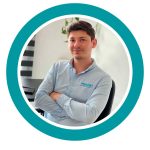
Written by: Ing Octavio Velazquez Rizo
Project manager
octavio@vemori.com